Reefgeorge
Well-known member
- Joined
- May 31, 2010
- Messages
- 563
- Status
- OWNER - I own a Hatteras Yacht
- Hatteras Model
- Not Currently A Hatteras Owner
This is one of my cockpit sole fish boxes. The two end lids are screwed into the stationary center section using piano hinges. The hinge screws are all pulling out of the center section. I started drilling out the holes ready to do the allen wrench and drill clean out followed by injecting something like S10 to be able to re dril and be done with it. What I found is that it is completely hollow behind the fiberglass and gelcoat veneer. Looks like I will need to come in from underneath the center brace with either individual holes and a backing material or cut out the entire length near the edge and bed in a length of material. What do You guys suggest?
Thanks,
George
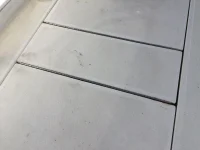
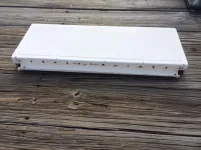
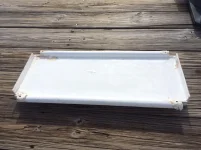
Thanks,
George
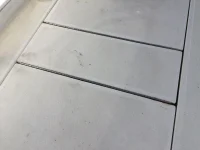
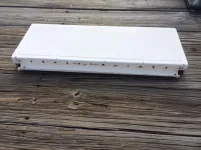
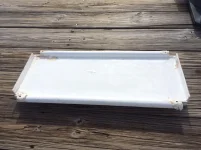
Last edited: